It’s apparently a boom time for space businesses in Australia. However, there are pieces of sovereign capability that are sorely missing, as David Doral explains in this part of our Fibres and composites transforming industry series.
We are seeing lately what could look like the beginning of a little space gold rush in Australia. Well, maybe that’s an exaggeration, if we imagine the real gold rush that will come someday, when rockets, launchers and other related space technology is ready to take us to other planets or asteroids to mine them for valuable resources.
The mini gold rush I am talking about refers to the attention space is generating among companies, federal and local governments and other types of organisations within Australia. I have personally witnessed it when attending the last editions of the Space Forum, held in Adelaide every 6 months, including the last one on March 21. It has gone from a small, free meet up with just a few dozen people to the last event attracting many hundreds, and having the Premier of South Australia and even the country’s Prime Minister as speakers.
To all the media attention we need to add the flow of funds coming from multiple grant programs, which is good news by the way, given the business case around many space commercial opportunities is initially marginal, with the hope of improving over time.
Currently no Australian manufacturer is providing large component fabrication and testing services to OEMs. The National Manufacturing Priority roadmap for space seems to emphasise nano and small satellites, as well as space components like sensors, critical subsystems and communication arrays. This looks like an apparent bias towards small componentry and systems.
But at the same time, sovereign capability to put payloads in space, including viable launch facilities, is also a priority of that roadmap. That capability can only be achieved if we do not rely completely on large structural components being shipped from overseas. Otherwise Australia will not be viable as a launch pad, due to the long distances and complicated logistics associated with shipping large space structures to this part of the world.
It would also be really disappointing and not particularly efficient in terms of using national resources if large satellite programs like JP9102 (but this is also applicable to independent rocket launchers developed by start-ups) rely on overseas manufacturing of large lightweight composite components.
We all know how critical weight reduction is in aerospace, and space launch structures and payloads are at the top of that list. Putting anything into orbit is an expensive exercise, with prices ranging between $50,000 and $100,000 per kg. A rule of thumb indicates you need to reduce 10kg of your launcher’s first stage to be able to add another kg of payload. But if you do it in your second stage that ratio becomes 1:1, that is to say, you save 1kg in your structure and you add 1kg to your payload. The dollar figures above refer to prices rather than costs, but if you are a company paying to put a satellite in space, managing to reduce the weight of your payload will translate directly into savings of that magnitude. But even for the launching company, reducing your weight will be similarly critical, particularly if you are planning to reuse your launcher.
This is worth a reminder, as developing a strong space industry ecosystem demands, among other things, a robust composites manufacturing capability. Fortunately this need has been identified in the Build phase of the Space National Manufacturing roadmap when we see that improving capability in lightweight structures is an area of focus.
As a successful aerospace composites manufacturer, we think that at Quickstep we have a role to play. Allow me the space literature reference when I say we think we have The Right Stuff in this endeavour to make a successful launch, bring it back to Earth and do it again. We are actually working in a bid to attract a package to manufacture space structures of significant size to Australia. We are leveraging our aerospace experience, capability and certifications to put in place the processes required to build these components, and yet we are finding that some of the capacity needs to be built ad hoc for space dimensions and requirements.
For instance, we will need to develop for the first time some of the procedures and equip ourselves with the systems required to test high acceleration, space vacuum and extreme temperature conditions suffered during a space launch and subsequent orbiting. We have tried to find domestically the kind of environmental chambers needed to simulate vacuum and thermal conditions in space, a requirement for some of the components we are planning to manufacture. Although some universities and research centres can provide that kind of capability to some extent, unfortunately what we have found is not suitable either because of size, temperature range or other requirements, and not enough for relatively large composite components.
This limitation is driving us to set up a plan to bring that capability in-house as the only viable option. Otherwise we would need to ship very large components across the globe to be tested overseas and then returned to Australia to complete the specified manufacturing sequence — something not only impractical but also uneconomical.
And this is for the largest independent composites manufacturer in Australia. Some of our industrial equipment is almost second to none, for example our main autoclave, which some argue might be the biggest in the Southern Hemisphere. And yet, space is bigger than that, if not for curing large composite panels (that we can do now), at least to test them.
This is where relevant support programs like the Modern Manufacturing Initiative (MMI) can really make a difference. Quickstep can play a role as a composites technology enabler for launchers and developers of large payloads, while at the same time the MMI can enable us to do it, by supporting financial efforts that will take way longer to provide returns than typically acceptable for a commercial company. The combined action of federal (and local if applicable) financial support programs like the MMI in its different streams will make possible and augment the efforts industry can make, yielding a strategically transformational effect.
This is the way to develop a strong ecosystem, and only like this will the Australian space industry reach critical mass or, more appropriately, escape velocity to get into orbit and become a real commercial reality, generating jobs and returns for the country.
Picture: supplied
David Doral is CTO and Head of Engineering at Quickstep.
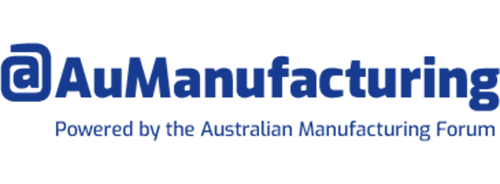
@AuManufacturing’s editorial series – fibres and composites transforming industry – is brought to you with the support of ThermoFisher Scientific and the Advanced Fibre Cluster Geelong.
Apr 2021